Hydraulic vs. Pneumatic Directional Control Valves: A Comparison
- infoairmaxpneumati
- Sep 26, 2023
- 3 min read
Hydraulic and pneumatic directional control valves are essential components in fluid power systems, but they serve different purposes and have distinct characteristics. Hydraulic valves use pressurized fluid to control machinery, providing high force and precision. In contrast, pneumatic valves use compressed air, offering lower force but faster operation. Choosing between them depends on factors like application requirements, cost, and environmental considerations. While hydraulic systems excel in heavy-duty applications, pneumatic systems find favor in tasks requiring rapid, responsive movement. Understanding the differences helps in selecting the most suitable directional control valve for a specific job.
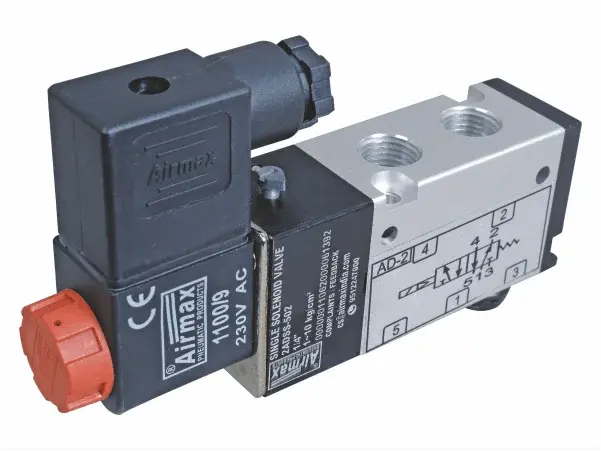
Operating Principles: Hydraulics and Pneumatics Unveiled
Hydraulic and pneumatic directional control valves operate on different principles, primarily distinguished by the fluids they use. Hydraulics utilize pressurized liquid, typically oil, while pneumatics employ compressed air. The basic concept shared by both systems is fluid power, which means using a fluid medium to transmit force.
In hydraulic systems, an electric motor or engine drives a pump to pressurize the hydraulic fluid. This pressurized fluid is then directed through hydraulic valves to control various components like cylinders and motors. Hydraulics excel in applications demanding high force and precision, such as heavy machinery, construction equipment, and aerospace systems.
Conversely, pneumatic systems utilize compressors to generate high-pressure air. This compressed air is routed through pneumatic valves to operate cylinders, actuators, and other components. Pneumatics are known for their speed and responsiveness, making them suitable for tasks requiring rapid movement, like robotics, packaging, and automotive assembly lines.
Strength and Precision: Force Comparison
One of the key distinctions between hydraulic and pneumatic directional control valves is the force they can exert. Hydraulics, due to the incompressible nature of hydraulic fluid, deliver significant force. This property is advantageous for applications involving heavy loads or precise control, such as lifting heavy machinery or molding processes.
On the other hand, pneumatics provide a lower force output compared to hydraulics. Compressed air is compressible, which means it can absorb some of the force applied to it. Therefore, pneumatic systems are better suited for tasks where lower force is acceptable, and where speed and responsiveness are essential.
Speed and Responsiveness: A Velocity Contrast
Hydraulic and pneumatic systems exhibit a stark contrast in terms of speed and responsiveness. Hydraulics are typically slower due to the viscosity of hydraulic fluid and the complexities of fluid dynamics. However, this slowness can be an advantage in certain applications requiring precise, controlled movements, like heavy machinery.
Pneumatics, on the other hand, are known for their rapid response times. Compressed air moves quickly, making pneumatics ideal for tasks that demand high-speed actuation and immediate response, such as automated assembly lines and pneumatic robotics.
Environmental Factors: Fluid Power System Considerations
Environmental factors play a significant role in choosing between hydraulic and pneumatic systems. Hydraulics use oil-based fluids, which can potentially leak and have environmental consequences if not managed properly. Controlling oil leaks is crucial to prevent pollution and ensure workplace safety.
In contrast, pneumatics use clean, non-toxic compressed air, making them more environmentally friendly. However, it's essential to manage air quality to prevent contaminants from entering the system, as they can impact performance and longevity.
Applications and Industry Preferences: Choosing the Right Valve Technology
The choice between hydraulic and pneumatic directional control valves ultimately depends on the specific requirements of the application. Certain industries have distinct preferences based on their needs:
Construction and Heavy Machinery: Industries like construction and mining often favor hydraulic systems for their high force capabilities, making them ideal for lifting, digging, and heavy-duty tasks.
Manufacturing and Automation: Manufacturing industries prefer pneumatic systems for their speed and responsiveness, which enhance efficiency in tasks like pick-and-place operations and assembly lines.
Aerospace and Defense: Aerospace and defense applications often utilize hydraulic systems for their precise control and ability to handle high loads in critical situations.
Medical Devices: Pneumatic systems are common in medical devices where cleanliness, precision, and rapid response are essential, such as in ventilators and surgical equipment.
In conclusion, understanding the operating principles, force capabilities, speed, environmental considerations, and industry preferences of hydraulic and pneumatic directional control valves is crucial for selecting the right technology for your specific application. Each has its unique strengths and limitations, and the choice should align with the operational demands and objectives of the given task or industry.
Comments